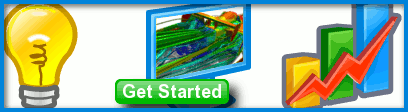
Sliver Treatment Strategies for CFD
Extremely thin, high-aspect-ratio geometry faces (also known as slivers) can cause problems for meshing and adversely affect Computational Fluid Dynamics (CFD) simulation stability. Learn some strategies to identify and deal with slivers to maximize your CFD productivity.
Sliver SurfaceProduces poor surface mesh elements (blue)
Identify Sliver
As with small feature detection, slivers are not always easy to identify.
Sliver Surface (Red)
An effective way to find slivers is to first generate a surface mesh, and then use mesh metrics with thresholding to identify highly stretched elements, which will tend to align themselves with the high aspect ratio surfaces.
Sliver Surface MeshCauses poor surface mesh elements (blue)
If left untreated the poor surface elements will lead to clusters of poor volume elements, which will likely cause your CFD simulation to either converge slowly or not at all.
Sliver Volume MeshCauses poor volume mesh element clusters (blue)
Having identified a sliver you have two options:
- Remove it.
- Retain it and improve the mesh element quality on it.
Remove Sliver
To remove a sliver you can simply join it with a larger neighbor such that the surface and volume mesh no longer need to conform to the surface edges.
Sliver Surface After Joining With Neighbor (Red)
Better Quality Surface Mesh After Sliver Removal
Retain Sliver
If you want to retain the sliver, e.g., as an inlet upon which you want to specify an inlet boundary condition, then you need to specify a mesh size constraint for the sliver that is typically within a factor of 1-3 times the width of the sliver.
Better Quality Surface Mesh After Adding Mesh Constraint
Recent blog posts
- CFD Simulates Distant Past
- Background on the Caedium v6.0 Release
- Long-Necked Dinosaurs Succumb To CFD
- CFD Provides Insight Into Mystery Fossils
- Wind Turbine Design According to Insects
- Runners Discover Drafting
- Wind Tunnel and CFD Reveal Best Cycling Tuck
- Active Aerodynamics on the Lamborghini Huracán Performante
- Fluidic Logic
- Stonehenge Vortex Revealed as April Fools' Day Distortion Field