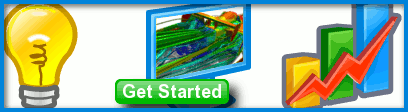
What is the most difficult part of CFD?
Submitted by symscape on February 13, 2012 - 16:25
Configuring Geometry
13% (18 votes)
Creating Mesh
37% (50 votes)
Deciding Physics
12% (16 votes)
Deciding Solver Controls
8% (11 votes)
Deciding Boundary Conditions
12% (16 votes)
Deciding Convergence Criteria
5% (7 votes)
Creating 3D Visualization
2% (3 votes)
Creating 2D Plots
0% (0 votes)
Extracting Integrated Values (e.g., Drag)
4% (5 votes)
Other
7% (9 votes)
Total votes: 135
Comments
meshing vs. geometry
Interesting that meshing is selected over geometry. Meshing should be a click of a button, given that the geometry is clean.
Difficult to differentiate between geometry and meshing
Yes, good point Derrek.
I think sometimes it's difficult to differentiate between geometry and meshing, and therefore often when geometry is the root cause of a problem instead it is cited as a meshing problem.
For example some CFD tools (e.g., mesh wrappers) don't clearly delineate between geometry and meshing. Such tools during the import process often immediately convert the geometry to facets (STL-like) and discard both the topology information and the true analytic description. In this case, by definition if there's a problem it has to be the meshing as far as a user is concerned, because the true geometry is long gone. In fact the initial conversion to facets is equivalent to a surface meshing stage that is hidden from the user, but it still has the scope to be either poor or wrong.
Yes, Derrek, you are right
Yes, Derrek, you are right about the geometry being a major pain for those who use a stand-alone tool. Back 10-11 years ago, when I worked in the aero industry, I had to take models from CATIA v4 through a CADfix program (not always a straight-forward process) to get it into Fluent. Also talking with John Cimbala over the summer while at a symposium held at Cornell, we discussed this geometry issue.
For those using a CAD embedded tool, the geometry is no sweat. Having not used SpaceClaim, I can not comment exactly, but I've heard that this can help greatly when using a third-party/stand-alone CFD tool. SolidWorks and Inventor can open many different files types as well, even if it is a dumb solid, so this has not been an issue for me in the most recent 10 years.
My vote was for meshing, more as a generality, because in my experience I feel that most people still struggle with this issue. This is not meant to be a shameless plug (SW employee), but I think the meshing capabilities in SW Flow Simulation (also known as Mentor Graphics' FloEFD) are outstanding! Full brick meshing and they've solved many of the issues with this approach. If not for anything, it would be worth your time to check it out for your overall knowledge of the industry. I would also be happy to show anyone the technology by emailing me at joe(at)galliera.us . I know that Eric Ahlstrom (google his name) was very impressed with it.
I would say there are 2
I would say there are 2 issues here. First, healing/cleaning/simplifying geometry. Second, generating a quality mesh that will give good results.
While there are some new surface wrapping techniques out now for "walking over" tiny geometry noogies and uglies, I would say that most CFD users out there still struggle with getting production geometry into mesh-worthy shape. The FloEFD approach is another good way to avoid some of these problems. In either case, your mileage will vary. Surface wrapping is great when it works, but even people with this capability often only go there as a last resort.
It's not just about getting a mesh, though. You have to get a quality mesh. That means refining the mesh in areas that will impact accuracy or convergence.
Take both together, and I'm sure this represents the biggest set of pains for would be CFD'ers.
Correlating with Actual Results
I picked "Other". Knowing how accurate your results are is always the hardest thing for me.
Most difficult part of CFD
To flow Joe's point check out the auto meshing in FlowSimulation aka FlowEFD. I once set-up and solved a problem in 3 days that took a brand F user 3 weeks to get the same answer due to mesh and geometry difficulties. The hardest thing for me is getting the correct boundary conditions from a customer. After that most of the time is spent compiling the results in an understandable format. Most analysis is still being used as a reactive tool - used proactively the cost is mostly incidental!